top of page


.png)
.png)
.png)
What is product simulation
A virtual product design validation process
Computer-based calculation
For estimating and verifying the product properties
(thermal, mechanical…) or comparing different designs

Evaluate the feasibility of the design throughout the whole product development stages
Accelerate the R&D process
Save the sample preparation time and cost

Why we need product simulation
What can we get from the product simulation
Thermal properties
Thermal resistance (℃/W)
Temperature plot
Fluid dynamics properties


1. Heatsink P-Q curve
2. Radiator P-Q curve
3. Fan P-Q curve
4. Pump P-Q curve

Mechanical properties
Product deformation under specific spring loading

What product can we simulate
Component level
1. Air cooler: 1U, 2U, 3U, active, passive, heat pipes, VC, etc.
2. Liquid cooler: cold plate, radiator, fans

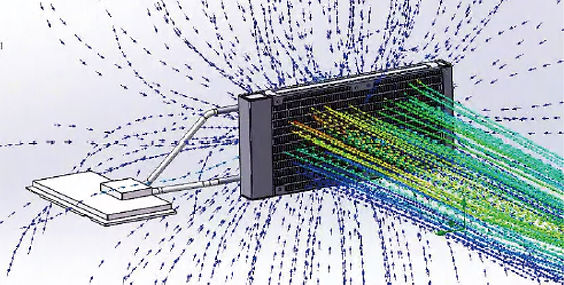
System level
1. Sever chassis
2. Sever cabinet
3. PC case
Information needed for the simulation
1. Product 3D design files (3D CAD)
2. Product materials specification
3. Environment: ambient temperature, air flow rate
4. Heater power and materials
5. Fan & pump properties if needed
6. Other specified information
A new simulation run is needed if any of the items above is changed.
Simulation time
3D file pre-processing and simulation environment set up
Usually 0.5 hrs.~2.5 hrs., depends on the product complexity
Component level simulation
Air cooler: Usually 10~30 mins for each run
Liquid cooler: Usually 1~3 hrs. for each run
System level simulation
Usually 4hrs. ~ 1 day for each run
Simulation procedure
1. Sales and engineers collect product requirement from the clients
2. Perform the product simulation run according to the product requirement
3. Send simulation results to client for reviewing
4. Revise the product and run the simulation if there’s any feedback from client
5. Physical sample prepare and test
6. Revise the product and run the simulation based on the physical sample test (if needed)
Case example(An air cooler project)
Client requirement: aim to beat a market model A
Simulation tools used when performing the
1. Thermal resistance simulation at the initial design stage
2. Fin pitch/thickness optimization
3. Fin tower size optimization
4. Heat pipe position arrangement optimization
Simulation results and physical sample test on the thermal resistance(℃/W)
